Variable speed drives can help solve India’s energy crisis
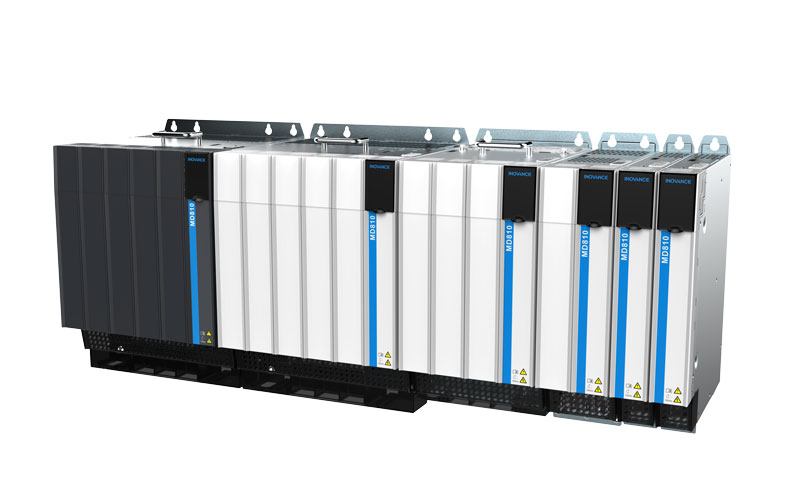
The energy problem
Like many countries across the globe, India is grappling with soaring energy costs. This is putting enormous pressure on the manufacturing industry, with energy being one of the largest costs for most factories (often, it is the single largest cost). The Ukraine-Russia conflict is responsible for the majority of this pressure. India is the world’s second largest coal importer but also imports around 80% of its crude oil as well as 45% of its natural gas. The conflict has pushed the price of these commodities to an all-time high. Not only does this impact the economic growth of the country, but it inhibits India’s ability to decarbonize.
Inovance Technology Europe provides some of the most sophisticated variable speed drive technology, allowing factories to slash their energy bills. The company is already supplying to many Indian manufacturers, helping them in their mission to both reduce costs in the short-term, and to reduce emissions so as to achieve climate change goals in the long-term.
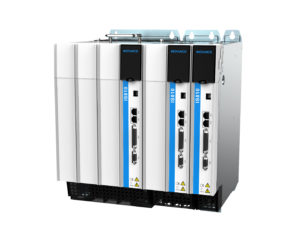
VSD’s bring big wins
Variable speed drives can bring many benefits to manufacturers. Energy saving is one of the most important. The largest savings are obtainable in simple applications, such as fans, pumps, and compressors, where energy savings from applying a basic drive can easily be 25% or more. In the case of a compressor, applying a VSD can often produce savings of up to 50%.
In India, there are still very many motors that are run ‘direct on line’ – i.e. plugged into the mains and run at full throttle all the time. The potential energy savings that many factories could make simply by making an assessment of all their motors, and applying drives wherever possible, are huge.
Energy saving tech
Inovance’s MD810, IS810 and MD800 all have a common feature: a common DC Bus – which contributes considerably to energy saving. The cost savings in a DC bus system come as a result of having a common rectifier which shares power to multiple motors. For more sophisticated applications, a regenerative rectifier with an active front end (AFE) can be used. The fact that the system uses a single, centralized component also provides significant energy savings by eliminating the need for multiple individual components. As well as this, a drive unit supplied from DC bus reduces the number of parts used, thereby reducing maintenance and repair costs.
For air compressor applications, Inovance’s CP700 drive brings many energy saving benefits. The technology complies with the IE2 efficiency standard whilst maintaining the most efficient operational capabilities. One recent Inovance compressor case study in India was a retrofit that involved a complete control solution – not only an AC drive but also a PLC, and an HMI. The result was radically improved energy efficiency and performance. Finally, the CS710 is an energy saving drive designed specifically for use in cranes to control asynchronous motors used for hoisting and travel with built-in functions like light load detection, pre-excitation, brake control logic etc.
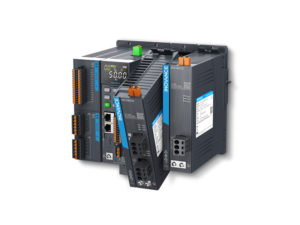
Environmental benefits
Not only is it important to save energy costs today, but it is equally important to slash carbon emissions for tomorrow. Investment in variable speed drives and other energy saving automation technologies helps to do just that. For example, Inovance has installed medium and low voltage drive systems in 114 steel enterprises globally, resulting in an annual reduction of 1,370,000 tons of carbon emissions, according to an internal study by the company.
It would arguably be logical to install more drives in most factories at any time. In the context of the current economic climate, it really is a no-brainer.
By: Mr.Anil Kumar,
Director, Inovance Technology India,