Utilization of weighing modules for load cells to avoid incorrect loading
For the most part incorrect loading can be avoided utilizing adequate mounting parts. The load cell and the mounting part together form a complex functional unit, a weighing module for load cells. HBM weighing modules come pre-assembled. They can instantly be installed and put into service on site without any additional measures being required. Depending on their type and mode of operation, weighing modules may include the following components:
- Upper and lower mounting plate for fastening onto a foundation or other carrier or superstructure
- Load application and output to the load cell
- Return to its original position in the event of side forces with pendulum bearings
- Damping of vibrations or dynamic loading using elastomer bearings
- Restraints against side force through horizontal stay rods
- Anti-liftoff device with simultaneous unloading of the module
Note: Not all weighing modules for load cells include all components specified. In part, they cannot be optionally retrofitted!
Configuration of weighing modules according to the application
Effects of mounting
Unevenness of the contact surface
Angle of inclination of the contact surface
The load cell’s sensitivity is reduced by 1-cosα. This deviation is compensated for via the weighing electronics during calibration of the weighing system. However, an angle of inclination of 3° must not be exceeded.
Plane parallelism
If base and top plate are not parallel to each other, this deviation of the force application parts from plane parallelism results in additional lateral force. This lateral force is absorbed in the longitudinal direction by the stay rod. In the transverse direction the pendulum support is deflected to such an extent that the equilibrium of forces is restored. However, to reduce the effect of lateral forces to a minimum, the angle of inclination must not under any circumstances exceed 3°.
Axial offset
An axial offset between cover plate and force application to the structure is acceptable since the plates are screwed together.
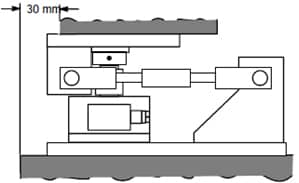