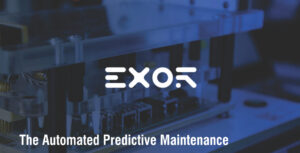
This article will discuss:
- Predictive maintenance as an Industrie 4.0 business model
- The benefits of automating predictive maintenance procedures
- Steps to automating predictive maintenance in industrial facilities
Everyone in the industrial manufacturing community has heard stories about downtime. But for those who have lived it, statistics such as one hour of downtime cost manufacturers up to $260,000 per hour or two million dollars in 4 hours do not tell the entire story. Aside from monetary losses, the actual cost of downtime includes a disillusioned workforce which becomes more difficult to motivate when persistent equipment failures occur. These are some of the reasons why the automation of predictive maintenance is fast becoming an industrial concept that enterprises integrate into everyday business operations.
Predictive maintenance as an Industrie 4.0 business model
Predictive maintenance involves taking a preemptive approach to discovering faults in, maintaining, and repairing factory equipment before it fails. As with every Industrie 4.0 concept, this approach also relies on data capture and analytics. Thus, the ability to understand the historical and current data a shop floor asset produces is the foundation for automating maintenance tasks at both component and assembly level.
Although predictive maintenance is an Industrie 4.0 concept, it still applies to both legacy and relatively new assets. According to
The Plant Engineer’s Handbook, predictive maintenance has the ability to reduce downtime by
approximately 20% while the option of automating the process can further increase this percentage and reduce unplanned downtime. The choice to integrate the automation of predictive maintenance across the shop floor also comes with many benefits which include:
1. Reduction in total manufacturing cost (TMC) – In manufacturing, maintenance costs, repairs, and costly replacements add up to a considerable proportion of the TMC of developing a product. Automating predictive maintenance helps reduce these costs in significant ways. These ways include having knowledge of a piece of equipment’s life span, scheduling planned downtimes, and planning inventory lists for spare parts.
Automated predictive maintenance initiatives lead to planned downtimes that reroute production away from affected equipment. They also eliminate the possibility of human errors in calculations which can delay the repair or maintenance activities associated with shop floor equipment. The automated process also comes with its own butterfly effect on an enterprise’s spare parts inventory. The knowledge of the task to be done can be used to automate the purchase of replacement parts ahead of time, thus reducing excessive stocking while ensuring the maintenance team has all the tools required for the task.
2. Increased service life of machine components – Automating regular predictive maintenance activities ensures the task is completed as and when due. The discipline of keeping to a strict schedule where maintenance is concerned increases the life span of components in a machine. This is because the machine and its components will be equipped with the resources needed to keep it running until the next maintenance cycle.
3. Reduced accidents on shop floors – In manufacturing facilities, material handling equipment is responsible for approximately 85 fatalities and thousands of injuries yearly in the US alone. These incidents occur due to dysfunctional forklifts, employee negligence, and more importantly, poorly maintained material handling equipment. This is where automating predictive maintenance activities come into play. With proper maintenance, material handling equipment and other engineering assets will function as expected without springing any surprises on unsuspecting shop floor workers.
Everyone in the industrial manufacturing community has heard stories about downtime. But for those who have lived it, statistics such as one hour of downtime cost manufacturers up to $260,000 per hour or two million dollars in 4 hours do not tell the entire story. Aside from monetary losses, the actual cost of downtime includes a disillusioned workforce which becomes more difficult to motivate when persistent equipment failures occur. These are some of the reasons why the automation of predictive maintenance is fast becoming an industrial concept that enterprises integrate into everyday business operations.
Predictive maintenance as an Industrie 4.0 business model
Predictive maintenance involves taking a preemptive approach to discovering faults in, maintaining, and repairing factory equipment before it fails. As with every Industrie 4.0 concept, this approach also relies on data capture and analytics. Thus, the ability to understand the historical and current data a shop floor asset produces is the foundation for automating maintenance tasks at both component and assembly level.
Although predictive maintenance is an Industrie 4.0 concept, it still applies to both legacy and relatively new assets. According to
The Plant Engineer’s Handbook, predictive maintenance has the ability to reduce downtime by
approximately 20% while the option of automating the process can further increase this percentage and reduce unplanned downtime. The choice to integrate the automation of predictive maintenance across the shop floor also comes with many benefits which include:
1. Reduction in total manufacturing cost (TMC) – In manufacturing, maintenance costs, repairs, and costly replacements add up to a considerable proportion of the TMC of developing a product. Automating predictive maintenance helps reduce these costs in significant ways. These ways include having knowledge of a piece of equipment’s life span, scheduling planned downtimes, and planning inventory lists for spare parts.
Automated predictive maintenance initiatives lead to planned downtimes that reroute production away from affected equipment. They also eliminate the possibility of human errors in calculations which can delay the repair or maintenance activities associated with shop floor equipment. The automated process also comes with its own butterfly effect on an enterprise’s spare parts inventory. The knowledge of the task to be done can be used to automate the purchase of replacement parts ahead of time, thus reducing excessive stocking while ensuring the maintenance team has all the tools required for the task.
2. Increased service life of machine components – Automating regular predictive maintenance activities ensures the task is completed as and when due. The discipline of keeping to a strict schedule where maintenance is concerned increases the life span of components in a machine. This is because the machine and its components will be equipped with the resources needed to keep it running until the next maintenance cycle.
3. Reduced accidents on shop floors – In manufacturing facilities, material handling equipment is responsible for approximately 85 fatalities and thousands of injuries yearly in the US alone. These incidents occur due to dysfunctional forklifts, employee negligence, and more importantly, poorly maintained material handling equipment. This is where automating predictive maintenance activities come into play. With proper maintenance, material handling equipment and other engineering assets will function as expected without springing any surprises on unsuspecting shop floor workers.

3 steps to automating predictive maintenance in manufacturing facilities
As with most manufacturing concepts or business models, steps to adopting an automated predictive maintenance culture exist. These steps include the following:
- Integrating data capture devices in equipment – The first step to automating predictive maintenance involves the capture of relevant data from the equipment. In greenfield facilities, the general manufacturing equipment used is equipped with sensors and actuators that monitor performance and the health of components. In brownfield facilities, data capture can only be achieved after the integration of smart devices into legacy equipment.
A smart human-machine interface device can be used to track the temperature, vibration, and other aspects of a piece of equipment on the shop floor. With these historical data in place, as well as downtime or failure-rate data, the process of automating predictive maintenance activities across a shop floor can be accomplished. The manufacturing enterprise will also need to set up industrial cloud solutions, analytical applications, and a functional ticketing or alert system to automate the predictive maintenance process.
- Algorithms to monitor patterns in real-time – For manufacturing enterprises just starting out, it is understandable that historical data that provide context into an equipment’s health is unavailable. This is where machine learning and artificial intelligence come into play. Enterprises will either need to purchase services or build applications powered by algorithms that enable condition-based monitoring. These services are among the applications highlighted in the first point in this section.It is also important to note that there are different techniques for assessing comparative machine data as the IT infrastructure kick-starts the process and the equipment collects data. Manufacturers can choose to purchase the related data from platforms offering Data as a Service to their industry niche or make extrapolations using the equipment’s repair or maintenance guide as a standard.
- A fundamental mind-set change to maintenance – The success of integrating automated predictive maintenance in a shop floor still depends on management and employee knowledge of predictive analysis. This is why the need to create a management and employee policy on automating predictive maintenance is important. Stakeholders within the four walls of the manufacturing outfit must understand what it takes to automate and the benefits it brings as highlighted above.
An enterprise’s success in integrating automated predictive maintenance relies on the commitment levels of the management team and employees. Only then can the automation process be successful as everyone understands their role within an automated manufacturing shop floor.
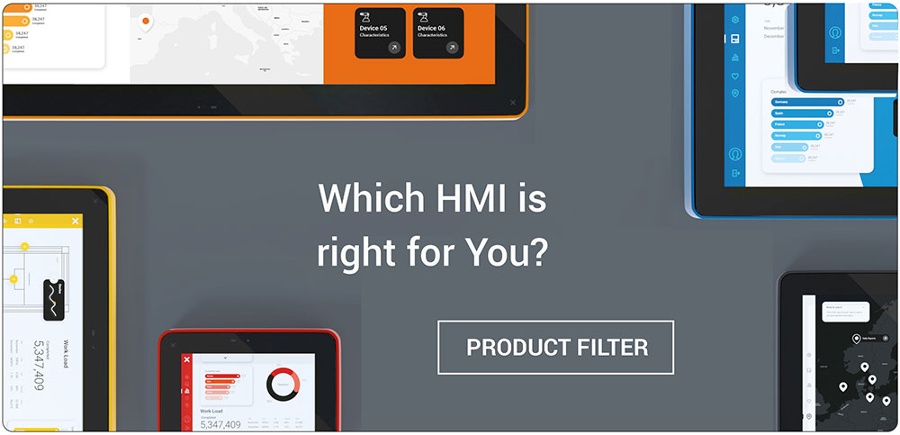
Conclusion
When automating predictive maintenance, the use of pilot programs to get everyone on the same page is recommended. If the automation is properly done, manufacturing organizations can reduce downtime by 55% and repair and overhaul time by approximately 60%. An effective maintenance culture will also reduce expenditure on equipment replacement while creating a conducive environment for increased productivity.